KI und andere Technologien
Crashsicherheit aktuell
22. Mai 2025 agvs-upsa.ch – Die Fahrzeugentwicklung funktioniert mehrheitlich digital. Von der statischen Konstruktion bis zu dynamischen, virtuellen Tests durchläuft ein neues Modell viele digitale Stationen, ehe vor Serienanlauf Prototypen gebaut werden. Um die passive Sicherheit weiter voranzutreiben, werden neue Technologien wie KI-Tools, Röntgenverfahren und andere Verfahren sowie moderne Werkstoffkombinationen eingesetzt. Andreas Senger
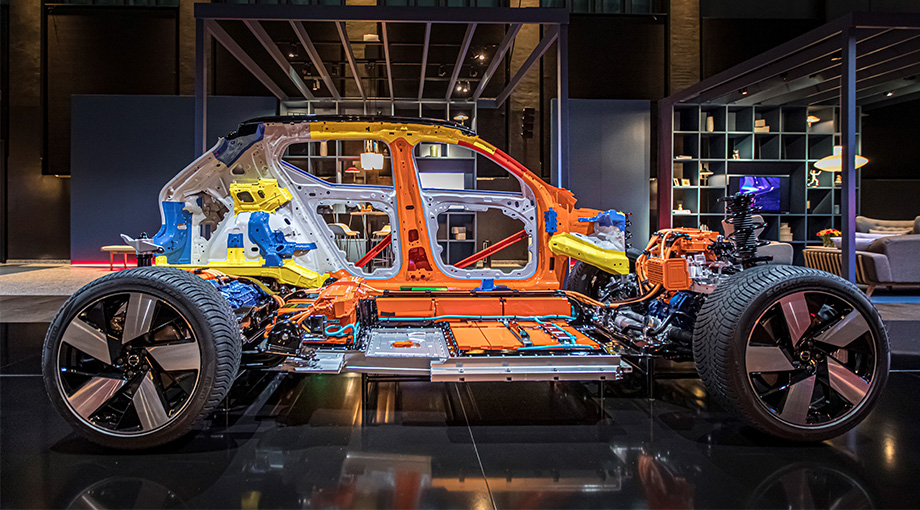
Auch batterieelektrische Fahrzeuge weisen eine hohe passive Sicherheit auf. Der Einsatz von verschiedenen, hochfesten Materialien bei der Sicherheitsfahrgastzelle und dem Batteriefach verhindert das Kollabieren. Lastpfade an Front und Heck in der Knautschzone wandeln Bewegungsenergie durch Deformation in Wärme um. Foto: Volvo
Automobile werden immer sicherer. Dank umfangreiche Fahrerassistenzsystemen wie Spurhalte-, Spurwechsel-, Notbrems-, Kreuzungs-, Linksabbiegeassistenten, aber auch Falschfahrerwarnungssystemen oder Lichtassistenzsystemen und anderen mehr ereignen sich im Grundsatz deutlich weniger gravierende Unfälle. Die aktiven Systeme unterstützen die Person hinter dem Lenkrad, um Unfälle zu vermeiden. Falls es trotzdem zum Unfall kommt, sorgen die passiven Sicherheitssysteme dafür, dass die Unfallfolgen wie Verletzungen der Insassen oder von aussen beteiligten Personen möglichst gering gehalten werden. Moderne Automobile verknüpfen die aktiven und passiven Systeme, um die Effizienz im Pre-Crash-Verhalten zu verbessern.
Die Software und damit die Verknüpfung der Systeme ersetzen eine konsequent auf Sicherheit ausgelegte Hardware – sprich Karosserie – nicht. In der Entwicklung werden die Karosserieteile Fahrgastsicherheitszelle möglichst steif und die Knautschzonen vorne und hinten möglichst energieabsorbierend und damit eher weich ausgelegt. Definierte Lastpfade an der Fahrzeugfront und am -heck wandeln kinetische Energie durch Deformation in Wärme um, Damit werden die Insassen mit biotechnisch verträglichen Verzögerungen abgebremst, so dass möglichst geringe Verletzungen resultieren. Dies geschieht im Verbund mit den Rückhaltesystemen (Gurt- und Gurtstraffer sowie Airbags), was ein Zusammenspiel von verschiedenen Systemen zur Folge hat. Unterschiedliche Werkstoffe wie hochfeste Stähle im Bereich der Fahrgastzelle und weichere Materialien wie Aluminium an Front und Heck unterstützen diese Bestrebungen. Immer mehr werden auch Verbundwerkstoffe eingesetzt, die eine geringe Dichte aufweisen und damit wenig Masse und trotzdem höchste Festigkeit besitzen.
Nach wie vor stellen Seitenaufprallunfälle eine grosse Challenge dar: Um auch die seitlich wirkende Bewegungs- in Wärmeenergie umzuwandeln, müssen Deformationspartien vorgesehen werden. Die Fahrzeuge sind deshalb in den vergangenen Jahren deutlich in der Breite gewachsen, um im Schweller- und Türenbereich energieabsorbierende Partien einzufügen. Vor allem bei batterieelektrischen Fahrzeugen stellt der Schutz der Hochvoltbatterie eine Herausforderung dar. Nebst der Intrusion (Eindringung) gilt es auch das Gehäuse so steif auszuführen, dass nicht durch Knickung Zellpakete verletzt und damit der gefürchtete «Thermal Runaway» gestartet wird. Die besten passiven Systeme nützen nichts, wenn die wenig verletzten, aber eventuell bewusstlosen Insassen nach dem Unfall durch einen Batteriebrand zusätzlich gefährdet werden.

Die Absicherung der virtuellen Crashtests am Computer erfolgt durch Crashversuche mit Prototypen. Die enorm teuren Versuchsträger können neu dank Röntgentechnologie während der Deformation auch in nicht sichtbaren Bereichen überwacht und die Simulationen verbessert sowie Optimierungen vorgenommen werden. Foto: Mercedes-Benz
Strukturanalyse im Detail und unter dem Blech
Der Übergang von deformierbaren Stellen zu möglichst steifen Partien sowie die möglichst gleichmässige Verzögerung der Insassen durch die definierten Lastpfade und deformierbaren Strukturen von allen Seiten fordern die Entwickler neuer Fahrzeuge heraus. Was am Computer durch Crashsimulationen und Korrektur in der Konstruktion schrittweise verbessert wird, kostet viel Zeit und Rechenpower. Deshalb findet KI vermehrt Einzug im Entwicklungsprozess. Dank künstlicher Intelligenz sind entsprechende Applikationen in der Lage, Konstruktionen auf Geometrie, Materialdicken und Werkstoff selbstständig zu optimieren, indem der Entwicklungsprozess durch automatisierte Iteration (Wiederholung durch Korrektur) ergänzt wird. Damit fliesst jahrzehntelange Erfahrung in der Fahrzeugentwicklung zusammen mit dynamischen und automatisierten Konstruktionstools, um die Fahrzeugstruktur für die passive Sicherheit zu verbessern und gleichzeitig die Fahrzeugmasse nicht ins Uferlose abdriften zu lassen.
Die Validierung der Simulation erfolgt schlussendlich immer mittels Prototypen, die aufwendig und noch von Hand zusammengebaut werden. Erste Prototypenteile von Zulieferern finden ebenso den Weg in diese Versuchsträger wie auch mittels 3D-Druck produzierte Fahrzeugteile. Die sündhaft teuren Prototypen werden auf der Strasse und in unterschiedlichen Regionen der Welt auf Herz und Nieren geprüft, um Temperaturbereiche, verschiedene Fahrbahnzustände und das Zusammenspiel der Fahrzeugsysteme zu erproben. Für die passive Sicherheit werden die Versuchsträger auch gecrasht. Dabei können mit einem Fahrzeug in mehreren Aufprallversuchen die Fahrzeugpartien geprüft werden. Der innerhalb von Millisekunden abgeschlossene Versuch zeigt dank Messpuppen (Dummies), wie hoch die Belastungen für die Fahrzeuginsassen war und welche Verletzungen resultieren würden. Zu erkennen, welche Partien jetzt aber noch für einen letzten Feinschliff optimiert werden können, setzt neuartige Technologien voraus. Für diesen Zweck hat Mercedes-Benz beispielsweise zusammen mit dem Fraunhofer Institut ein Röntgengerät entwickelt, das beim Crash das Fahrzeug mit 1000 Bildern pro Sekunden «durchleuchtet». Mit dieser neuen Technologie lassen sich erstmals Bilder von verborgenen Fahrzeugstrukturen (unter der Aussenhaut) sowie die Körper der Dummies im Detail und in Verlangsamung auswerten. Nebst den Hochgeschwindigkeitskameras, welche den Blick auf das Äussere richten, können mit der Radartechnologie schnellablaufende Prozesse auch in nicht einsehbaren Bereichen visualisiert werden. Für Laien sind die Bilder nichtsaussagend. Die Entwickler können aber dank dieser Bilder die Validierung der virtuellen Crashs optimaler ausführen und die Programmierung anpassen.
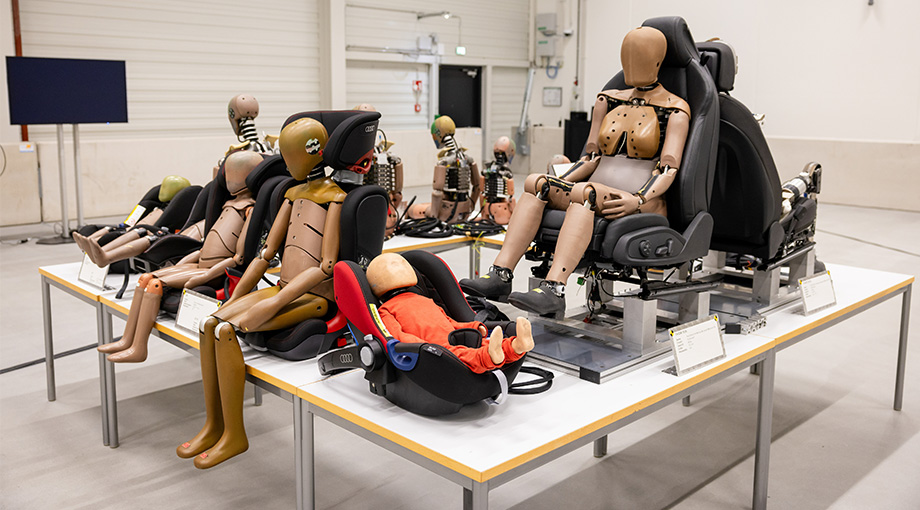
Die Dummy-Familie erlaubt die Aufnahme von unzähligen Parametern während des Crashs und die Optimierung von Rückhaltesystemen von Klein bis Gross. Foto: Audi
Sie halten trotzdem für uns den Kopf hin
Obwohl mittlerweile viel am Computer getestet und geprüft werden kann, sind reale Crashtest mit Parametererfassung unerlässlich. Nebst der erwähnten Bildauswertung liefern Sensoren Beschleunigungs- und Gierratenwerte (g-Kräfte) in allen drei Fahrzeugachsen. Um die Auswirkungen auf die Insassen zu eruieren, werden Dummies platziert, die biomechanisch den Körperaufbau eines Menschen simulieren. Die Messpuppen besitzen ebenfalls eine Vielzahl von Sensoren, deren Auswertung Rückschlüsse auf Verletzungsschwere und Beanspruchung des Skeletts, der Muskeln und der inneren Organe zulässt. Um auch äusserliche Verletzungen und beispielsweise Berührungspunkte mit Fahrzeugteilen wie Lenkrad, Armaturenträger oder Türe festzustellen, werden Partien mit spezieller Farbe versehen, welche am Fahrzeug nach dem Unfall Spuren hinterlassen. Um möglichst viele Menschen abbilden zu können, verfügen die Automobilhersteller über eine Vielzahl verschiedenster Dummies in allen Grössen und Formen. Die Rückhaltesysteme müssen die leichtgewichtigen bis adipösen Personen und kleingewachsene Menschen bis zu Grossgewachsenen schützen können. Auch Kinderpuppen in verschiedenen Ausführungen sorgen für eine möglichst realistische Abbildung.
Die Dummies haben ebenfalls virtuelle Kolleginnen und Kollegen. Die Abbildung des Körperaufbaus eines Menschen ist sowohl für die Fertigung der Puppen wie auch für die Programmierung für die Crashsimulationen aufwendig. Deshalb sind die Applikationen und der Aufwand für die Verbesserung der virtuellen Crashtests kostenintensiv. Die Simulation ist aber gerade für Neuentwicklungen unter dem Strich lohnender, da die Präzision zunimmt und unterschiedlichste Fahrzeugkonzepte und -entwicklungen ohne Protoypenbau geprüft werden können.
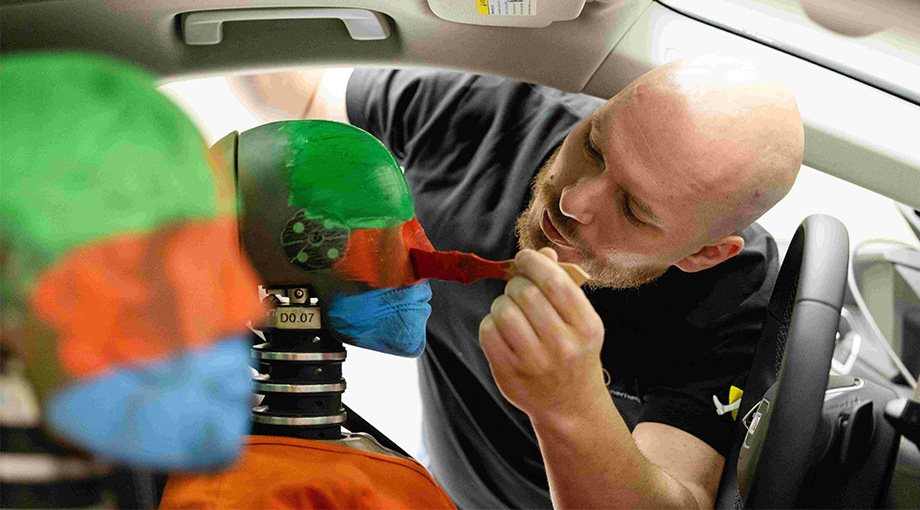
Ein Mitarbeiter färbt Stellen der Dummies ein, um die Aufprallorte während des Crashversuches im Innenraum optisch sichtbar zu machen. Foto: Audi
Verschmelzung der Sicherheitssysteme
Die eingangs erwähnte Systemvernetzung von aktiver und passiver Sicherheit reduziert insbesondere für ungeschützte Verkehrsteilnehmende die Verletzungsgefahr erheblich. Dabei spielt die Umfeldanalyse eine zentrale Rolle. Erfasst die Frontkamera beispielsweise einen E-Trottinett-Fahrer, der sich seitlich vor das eigene Fahrzeug bewegt, reagiert ein modernes Automobil mit einem Notbremseingriff. Der Verkehrsteilnehmende wird von der Frontkamera erfasst, das Bewegungsprofil erstellt und wegen einer drohenden Kollision der Notbremsassistent aktiviert. Ist der Weg zu kurz für eine Unfallvermeidung, sorgt das Auslösen der pyrotechnischen Aktoren zur Motorhauben- Anhebung und die vom Gesetzgeber vorgegebene, weiche Fahrzeugfront für ein sanfteres Aufnehmen des Kollisionsgegners.
Die Vernetzung von aktiver und passiver Sicherheit wird dank der Umfeldüberwachung durch Sensoren noch deutliche Verbesserungen erfahren und Bewegungsvorhersagen das Verkehrsgeschehen auch für die Systeme lesbar machen. Ein Übersehen von anderen Verkehrsteilnehmern, wie dies dem Menschen aufgrund der begrenzten Wahrnehmungsfrequenz passieren kann, ist für Hard- und Software des Fahrzeuges undenkbar. Menschen erfassen rund drei Verkehrssituationen pro Sekunde. Die Fahrerassistenzsysteme sind quasi rund um das Fahrzeug permanent und dank Sensordatenfusion auch redundant am Auswerten.
Dass bei den neuen Antriebssystemen noch Optimierungspotenzial besteht, verdeutlicht die Physik: Je höher das Fahrzeuggewicht und je mehr Batteriemasse mitgeführt wird, desto höher ist die Reichweite, aber gleichzeitig auch die kinetische Energie. Der Spagat zwischen passiver Sicherheit von Hochvoltbatterien und der Reduktion der Masse des Energiespeichers bieten noch viel Entwicklungspotenzial. Deshalb ist insbesondere der Bereich der Hochvoltbatterie für die passive Sicherheit ein interessantes Forschungs- und Entwicklungsfeld: Die Batteriekästen sollen möglichst steif sein und die Zellen schützen, aber trotzdem wenig Masse aufweisen.
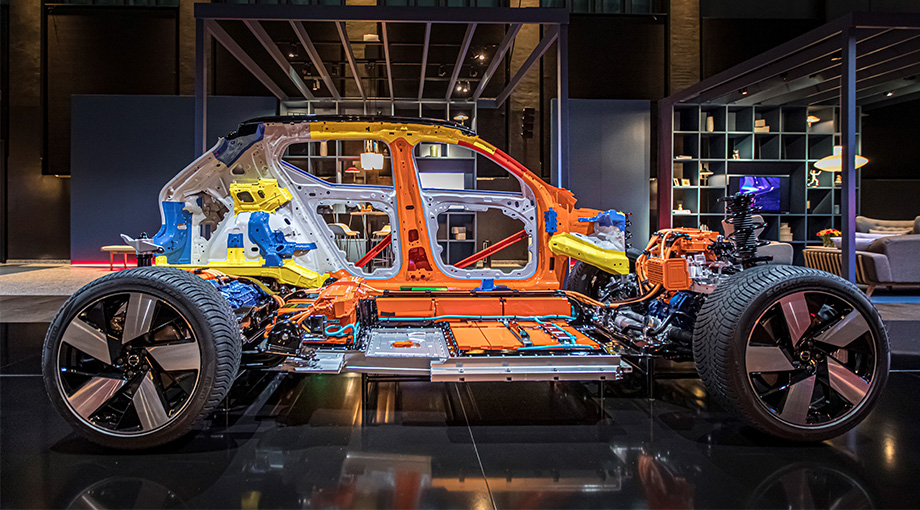
Auch batterieelektrische Fahrzeuge weisen eine hohe passive Sicherheit auf. Der Einsatz von verschiedenen, hochfesten Materialien bei der Sicherheitsfahrgastzelle und dem Batteriefach verhindert das Kollabieren. Lastpfade an Front und Heck in der Knautschzone wandeln Bewegungsenergie durch Deformation in Wärme um. Foto: Volvo
Automobile werden immer sicherer. Dank umfangreiche Fahrerassistenzsystemen wie Spurhalte-, Spurwechsel-, Notbrems-, Kreuzungs-, Linksabbiegeassistenten, aber auch Falschfahrerwarnungssystemen oder Lichtassistenzsystemen und anderen mehr ereignen sich im Grundsatz deutlich weniger gravierende Unfälle. Die aktiven Systeme unterstützen die Person hinter dem Lenkrad, um Unfälle zu vermeiden. Falls es trotzdem zum Unfall kommt, sorgen die passiven Sicherheitssysteme dafür, dass die Unfallfolgen wie Verletzungen der Insassen oder von aussen beteiligten Personen möglichst gering gehalten werden. Moderne Automobile verknüpfen die aktiven und passiven Systeme, um die Effizienz im Pre-Crash-Verhalten zu verbessern.
Die Software und damit die Verknüpfung der Systeme ersetzen eine konsequent auf Sicherheit ausgelegte Hardware – sprich Karosserie – nicht. In der Entwicklung werden die Karosserieteile Fahrgastsicherheitszelle möglichst steif und die Knautschzonen vorne und hinten möglichst energieabsorbierend und damit eher weich ausgelegt. Definierte Lastpfade an der Fahrzeugfront und am -heck wandeln kinetische Energie durch Deformation in Wärme um, Damit werden die Insassen mit biotechnisch verträglichen Verzögerungen abgebremst, so dass möglichst geringe Verletzungen resultieren. Dies geschieht im Verbund mit den Rückhaltesystemen (Gurt- und Gurtstraffer sowie Airbags), was ein Zusammenspiel von verschiedenen Systemen zur Folge hat. Unterschiedliche Werkstoffe wie hochfeste Stähle im Bereich der Fahrgastzelle und weichere Materialien wie Aluminium an Front und Heck unterstützen diese Bestrebungen. Immer mehr werden auch Verbundwerkstoffe eingesetzt, die eine geringe Dichte aufweisen und damit wenig Masse und trotzdem höchste Festigkeit besitzen.
Nach wie vor stellen Seitenaufprallunfälle eine grosse Challenge dar: Um auch die seitlich wirkende Bewegungs- in Wärmeenergie umzuwandeln, müssen Deformationspartien vorgesehen werden. Die Fahrzeuge sind deshalb in den vergangenen Jahren deutlich in der Breite gewachsen, um im Schweller- und Türenbereich energieabsorbierende Partien einzufügen. Vor allem bei batterieelektrischen Fahrzeugen stellt der Schutz der Hochvoltbatterie eine Herausforderung dar. Nebst der Intrusion (Eindringung) gilt es auch das Gehäuse so steif auszuführen, dass nicht durch Knickung Zellpakete verletzt und damit der gefürchtete «Thermal Runaway» gestartet wird. Die besten passiven Systeme nützen nichts, wenn die wenig verletzten, aber eventuell bewusstlosen Insassen nach dem Unfall durch einen Batteriebrand zusätzlich gefährdet werden.

Die Absicherung der virtuellen Crashtests am Computer erfolgt durch Crashversuche mit Prototypen. Die enorm teuren Versuchsträger können neu dank Röntgentechnologie während der Deformation auch in nicht sichtbaren Bereichen überwacht und die Simulationen verbessert sowie Optimierungen vorgenommen werden. Foto: Mercedes-Benz
Strukturanalyse im Detail und unter dem Blech
Der Übergang von deformierbaren Stellen zu möglichst steifen Partien sowie die möglichst gleichmässige Verzögerung der Insassen durch die definierten Lastpfade und deformierbaren Strukturen von allen Seiten fordern die Entwickler neuer Fahrzeuge heraus. Was am Computer durch Crashsimulationen und Korrektur in der Konstruktion schrittweise verbessert wird, kostet viel Zeit und Rechenpower. Deshalb findet KI vermehrt Einzug im Entwicklungsprozess. Dank künstlicher Intelligenz sind entsprechende Applikationen in der Lage, Konstruktionen auf Geometrie, Materialdicken und Werkstoff selbstständig zu optimieren, indem der Entwicklungsprozess durch automatisierte Iteration (Wiederholung durch Korrektur) ergänzt wird. Damit fliesst jahrzehntelange Erfahrung in der Fahrzeugentwicklung zusammen mit dynamischen und automatisierten Konstruktionstools, um die Fahrzeugstruktur für die passive Sicherheit zu verbessern und gleichzeitig die Fahrzeugmasse nicht ins Uferlose abdriften zu lassen.
Die Validierung der Simulation erfolgt schlussendlich immer mittels Prototypen, die aufwendig und noch von Hand zusammengebaut werden. Erste Prototypenteile von Zulieferern finden ebenso den Weg in diese Versuchsträger wie auch mittels 3D-Druck produzierte Fahrzeugteile. Die sündhaft teuren Prototypen werden auf der Strasse und in unterschiedlichen Regionen der Welt auf Herz und Nieren geprüft, um Temperaturbereiche, verschiedene Fahrbahnzustände und das Zusammenspiel der Fahrzeugsysteme zu erproben. Für die passive Sicherheit werden die Versuchsträger auch gecrasht. Dabei können mit einem Fahrzeug in mehreren Aufprallversuchen die Fahrzeugpartien geprüft werden. Der innerhalb von Millisekunden abgeschlossene Versuch zeigt dank Messpuppen (Dummies), wie hoch die Belastungen für die Fahrzeuginsassen war und welche Verletzungen resultieren würden. Zu erkennen, welche Partien jetzt aber noch für einen letzten Feinschliff optimiert werden können, setzt neuartige Technologien voraus. Für diesen Zweck hat Mercedes-Benz beispielsweise zusammen mit dem Fraunhofer Institut ein Röntgengerät entwickelt, das beim Crash das Fahrzeug mit 1000 Bildern pro Sekunden «durchleuchtet». Mit dieser neuen Technologie lassen sich erstmals Bilder von verborgenen Fahrzeugstrukturen (unter der Aussenhaut) sowie die Körper der Dummies im Detail und in Verlangsamung auswerten. Nebst den Hochgeschwindigkeitskameras, welche den Blick auf das Äussere richten, können mit der Radartechnologie schnellablaufende Prozesse auch in nicht einsehbaren Bereichen visualisiert werden. Für Laien sind die Bilder nichtsaussagend. Die Entwickler können aber dank dieser Bilder die Validierung der virtuellen Crashs optimaler ausführen und die Programmierung anpassen.
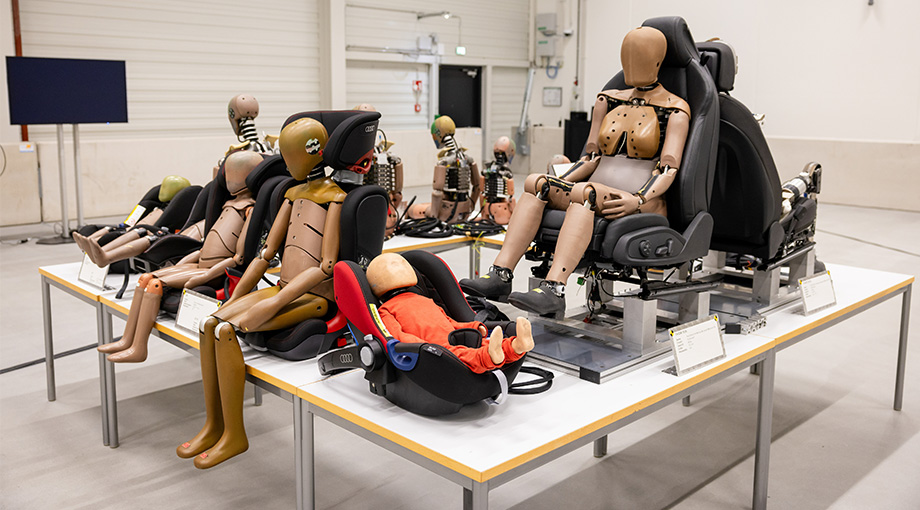
Die Dummy-Familie erlaubt die Aufnahme von unzähligen Parametern während des Crashs und die Optimierung von Rückhaltesystemen von Klein bis Gross. Foto: Audi
Sie halten trotzdem für uns den Kopf hin
Obwohl mittlerweile viel am Computer getestet und geprüft werden kann, sind reale Crashtest mit Parametererfassung unerlässlich. Nebst der erwähnten Bildauswertung liefern Sensoren Beschleunigungs- und Gierratenwerte (g-Kräfte) in allen drei Fahrzeugachsen. Um die Auswirkungen auf die Insassen zu eruieren, werden Dummies platziert, die biomechanisch den Körperaufbau eines Menschen simulieren. Die Messpuppen besitzen ebenfalls eine Vielzahl von Sensoren, deren Auswertung Rückschlüsse auf Verletzungsschwere und Beanspruchung des Skeletts, der Muskeln und der inneren Organe zulässt. Um auch äusserliche Verletzungen und beispielsweise Berührungspunkte mit Fahrzeugteilen wie Lenkrad, Armaturenträger oder Türe festzustellen, werden Partien mit spezieller Farbe versehen, welche am Fahrzeug nach dem Unfall Spuren hinterlassen. Um möglichst viele Menschen abbilden zu können, verfügen die Automobilhersteller über eine Vielzahl verschiedenster Dummies in allen Grössen und Formen. Die Rückhaltesysteme müssen die leichtgewichtigen bis adipösen Personen und kleingewachsene Menschen bis zu Grossgewachsenen schützen können. Auch Kinderpuppen in verschiedenen Ausführungen sorgen für eine möglichst realistische Abbildung.
Die Dummies haben ebenfalls virtuelle Kolleginnen und Kollegen. Die Abbildung des Körperaufbaus eines Menschen ist sowohl für die Fertigung der Puppen wie auch für die Programmierung für die Crashsimulationen aufwendig. Deshalb sind die Applikationen und der Aufwand für die Verbesserung der virtuellen Crashtests kostenintensiv. Die Simulation ist aber gerade für Neuentwicklungen unter dem Strich lohnender, da die Präzision zunimmt und unterschiedlichste Fahrzeugkonzepte und -entwicklungen ohne Protoypenbau geprüft werden können.
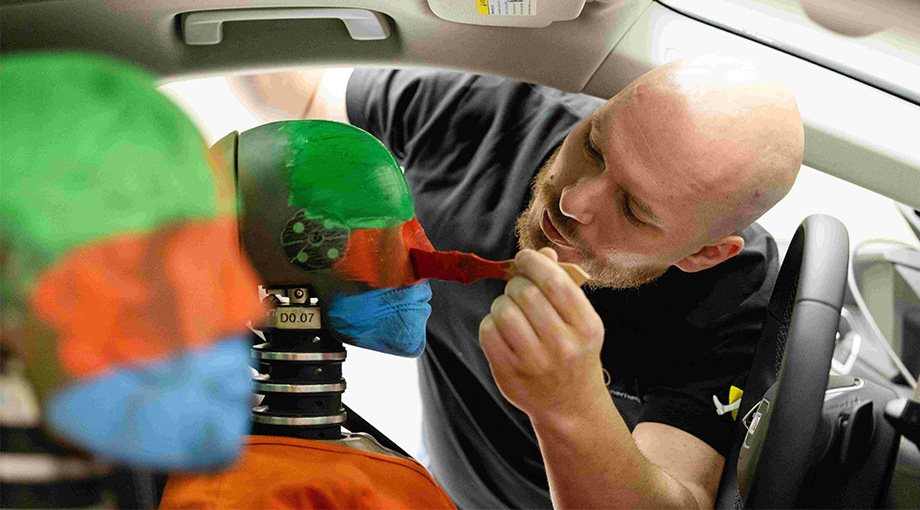
Ein Mitarbeiter färbt Stellen der Dummies ein, um die Aufprallorte während des Crashversuches im Innenraum optisch sichtbar zu machen. Foto: Audi
Verschmelzung der Sicherheitssysteme
Die eingangs erwähnte Systemvernetzung von aktiver und passiver Sicherheit reduziert insbesondere für ungeschützte Verkehrsteilnehmende die Verletzungsgefahr erheblich. Dabei spielt die Umfeldanalyse eine zentrale Rolle. Erfasst die Frontkamera beispielsweise einen E-Trottinett-Fahrer, der sich seitlich vor das eigene Fahrzeug bewegt, reagiert ein modernes Automobil mit einem Notbremseingriff. Der Verkehrsteilnehmende wird von der Frontkamera erfasst, das Bewegungsprofil erstellt und wegen einer drohenden Kollision der Notbremsassistent aktiviert. Ist der Weg zu kurz für eine Unfallvermeidung, sorgt das Auslösen der pyrotechnischen Aktoren zur Motorhauben- Anhebung und die vom Gesetzgeber vorgegebene, weiche Fahrzeugfront für ein sanfteres Aufnehmen des Kollisionsgegners.
Die Vernetzung von aktiver und passiver Sicherheit wird dank der Umfeldüberwachung durch Sensoren noch deutliche Verbesserungen erfahren und Bewegungsvorhersagen das Verkehrsgeschehen auch für die Systeme lesbar machen. Ein Übersehen von anderen Verkehrsteilnehmern, wie dies dem Menschen aufgrund der begrenzten Wahrnehmungsfrequenz passieren kann, ist für Hard- und Software des Fahrzeuges undenkbar. Menschen erfassen rund drei Verkehrssituationen pro Sekunde. Die Fahrerassistenzsysteme sind quasi rund um das Fahrzeug permanent und dank Sensordatenfusion auch redundant am Auswerten.
Dass bei den neuen Antriebssystemen noch Optimierungspotenzial besteht, verdeutlicht die Physik: Je höher das Fahrzeuggewicht und je mehr Batteriemasse mitgeführt wird, desto höher ist die Reichweite, aber gleichzeitig auch die kinetische Energie. Der Spagat zwischen passiver Sicherheit von Hochvoltbatterien und der Reduktion der Masse des Energiespeichers bieten noch viel Entwicklungspotenzial. Deshalb ist insbesondere der Bereich der Hochvoltbatterie für die passive Sicherheit ein interessantes Forschungs- und Entwicklungsfeld: Die Batteriekästen sollen möglichst steif sein und die Zellen schützen, aber trotzdem wenig Masse aufweisen.
Kommentar hinzufügen
Kommentare